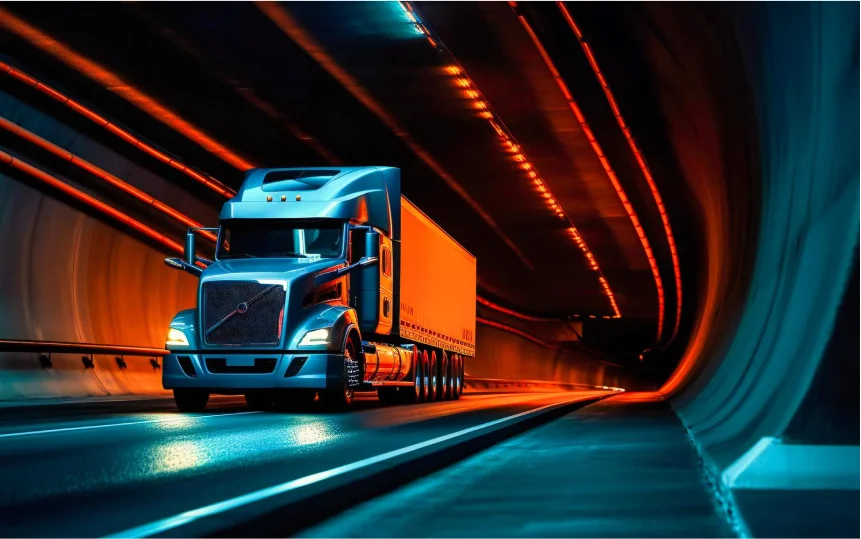
Automated Forklifting
Automated forklifting, the use of robotic or automated systems to handle material lifting and transport tasks, is revolutionizing warehouse and logistics operations. By integrating advanced technologies, such as robotics, sensors, and artificial intelligence, automated forklifting offers numerous benefits that enhance efficiency, safety, and overall operational effectiveness. Here’s why automated forklifting is becoming increasingly important:
1. Increased Efficiency and Productivity
Automated forklifts can operate continuously, without the need for breaks or downtime. This leads to higher productivity as they streamline material handling processes, from picking and transporting to stacking and sorting. With faster and more precise operations, automated forklifts help reduce order processing times and improve overall workflow efficiency.
2. Enhanced Safety
Automated forklifts reduce the risk of workplace accidents and injuries associated with manual material handling. They are equipped with advanced sensors and safety features that prevent collisions and detect obstacles, ensuring safe operation around human workers and other equipment. By minimizing human involvement in potentially hazardous tasks, automated forklifts contribute to a safer working environment.
3. Cost Savings
While the initial investment in automated forklifting systems can be significant, the long-term cost savings are substantial. Automated systems reduce labor costs by minimizing the need for manual operators and can lead to fewer workplace injuries, which lowers insurance and compensation costs. Additionally, increased efficiency and reduced operational errors contribute to overall cost savings and a better return on investment.
4. Improved Accuracy and Consistency
Automated forklifts offer precise control and consistent performance, which enhances accuracy in material handling tasks. They follow predefined paths and protocols, reducing the likelihood of human errors such as misplacing or damaging goods. This accuracy leads to improved inventory management, fewer errors in order fulfillment, and enhanced customer satisfaction.
5. Optimized Space Utilization
Automated forklifts can operate in tight and complex warehouse environments, utilizing vertical space more effectively. They are often designed to navigate narrow aisles and high racking systems, allowing for denser storage configurations. This optimized space utilization can increase warehouse capacity and improve the overall organization of inventory.
6. Scalability and Flexibility
Automated forklifts can be integrated into existing warehouse systems and scaled according to operational needs. As businesses grow and demand fluctuates, automated systems can be adjusted or expanded to accommodate changes in volume and complexity. This flexibility ensures that material handling operations can adapt to evolving business requirements.
7. Enhanced Data Collection and Analytics
Automated forklifts are equipped with sensors and data collection capabilities that provide valuable insights into warehouse operations. They can track metrics such as handling times, inventory levels, and equipment usage. This data is essential for analyzing performance, identifying areas for improvement, and making informed decisions to optimize operations.
8. Reduced Human Error
Automation reduces the potential for human error, which can occur due to fatigue, distraction, or misjudgment. Automated forklifts follow precise algorithms and programming, ensuring consistent and accurate performance. This reduction in errors enhances the reliability of material handling processes and contributes to overall operational efficiency.
9. Integration with Warehouse Management Systems (WMS)
Automated forklifts can be seamlessly integrated with Warehouse Management Systems (WMS) and other logistics technologies. This integration allows for real-time coordination and communication between automated systems and warehouse management software. It enables more efficient scheduling, inventory tracking, and overall management of warehouse operations.
10. Future-Proofing Operations
Investing in automated forklifting technology positions businesses for future advancements in warehouse automation. As technology continues to evolve, automated systems can be upgraded with new features and capabilities, ensuring that operations remain competitive and up-to-date with industry standards.